In recent years, a new type of robot, the cable-driven robot, has drawn attention from researchers and the industry. A cable-driven robot is a mechanism that possess a set of unique advantages, in particular their ability to span large spaces while carrying heavy loads and remaining simple in structure in a way that other types of robots cannot. It has been used for a range of interesting applications, including building construction, search and rescue, radio telescopes, logistics and many more.
This project explores the development of a new class of lightweight and portable systems that are able to operate in large spaces. This has interesting applications within art and architecture, where portability and ease of setup is important as demonstrations at different locations are typically expected.
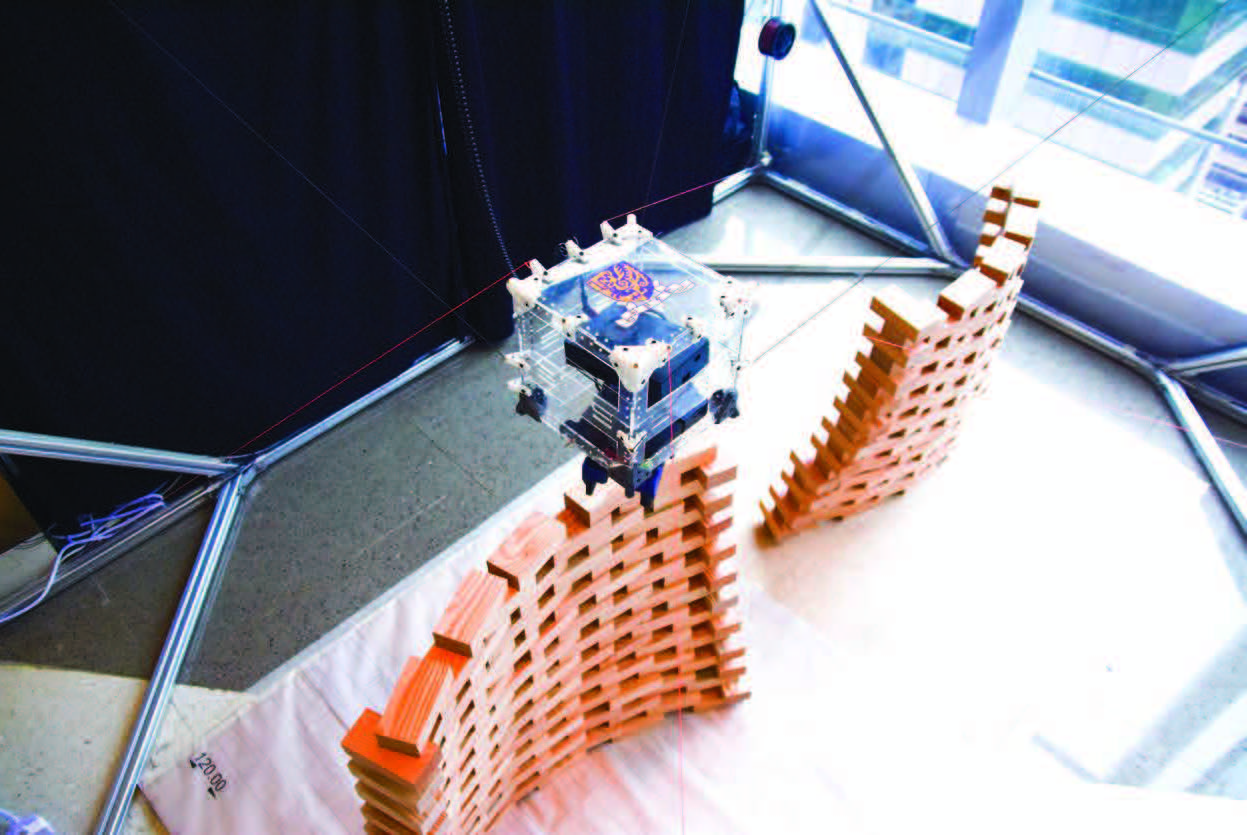
CU-Brick display in 2017 Bi-City Biennale of Urbanism\Architecture (Hong Kong) exhibitions
DESIGN AND ANALYSIS OF PORTABLE CABLE-DRIVEN ROBOT
An important unique characteristic of cable-driven robots is that cables can only pull and not push, resulting in challenges to the modelling, analysis, design and control of this class of system. There exists a wide range of different structures of cable-driven robots that require different modelling techniques.
The project development must overcome several challenges. Firstly, the cable actuators of the system need to be made more compact. In addition to the hardware and software developments, the actuators size requires analysis on the force-speed capabilities of the resulting robot with a significant impact on the design and selection of motors, and also generation of trajectory in order to comply with the capabilities of the motors due to the coupling between the force and speed of the system.
Second, the calibration of the system is critical in order for it to achieve the desired accuracy as the robot does not initially know its own position. A new method is proposed to perform auto-calibration based on collecting a sequence of feedback of the length of the cables for some random motion of the system [3].

Display as part of the 2017 Hong Kong Bi-City Biennale of Urbanism/Architecture
INTELLIGENT DESIGN AND ART/ARCHITECTURE APPLICATIONS
With the advantages in autonomy of robots, collaboration with different departments in arts and architecture has sparked work in the intelligence of the design process such that the entire system can be autonomous from design to execution. Two different applications will be presented in the following: 1) design and pre-fabrication of inflatable structures; and 2) CU-Brick robot to construct geometrically complex brick structures.
The goal of inflatable structures is to design aesthetically pleasing structures that take form through inflation. In this work, the desired resulting structure is first designed using CAD software. Next, the structure is computationally deconstructed into individual segments/strips to be fabricated by the cable-driven robot. Using the laser end-effector developed, the robot is then able to autonomously cut through thin sheets of plastic for each segment/strip [4]. The use of the portable cable-driven robot for this application is very suitable as lasers cutting on the scale of metres would be extremely bulky and expensive. By contrast, the developed system can easily be taken to different locations to fabricate the required segments.
The second example is a brick structure construction system ‘CU-Brick’, where the robot is able to autonomously construct geometrically complex brick structures with hundreds of bricks and more. The system consists of a gripper end-effector and the cable actuators can be mounted on metal frame structures to the walls and roofs of buildings, in a range of different environments. The design is performed through developed intelligent software where particularly parameters are provided, and it will then automatically generate the structure to be built, while remaining within the operational region of the robot and determined parameters such as the number and location of bricks, ensuring that the resulting structure is sufficiently stable.
Demonstrating the system’s portability and setup convenience, the CU-Brick system has been tested at a range of different locations, from the CUHK T-Stone Robotics Institute and School of Architecture, to public spaces such as Hysan Place where it is currently being displayed as part of the 2017 Hong Kong Bi-City Biennale of Urbanism/Architecture. It has also been shown outside of Hong Kong in Shenzhen and Beijing. The ability to carry the actuators of the system in a small suitcase opens up a range of possibilities in larger scale artistic displays that otherwise may have been too difficult to realise.
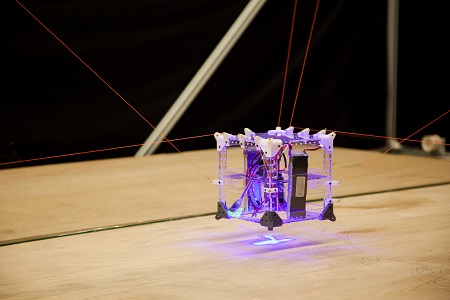
Portable cable-driven robot with a laser end-effector (robot named XL-Laser)
[1] D. LAU, D. OETOMO, and S. K. HALGAMUGE, “Generalised Formulation and Analysis of Multilink Parallel Cable-Driven Manipulators with Arbitrary Routing using Cable-Routing Matrix”, IEEE Transactions on Robotics, Vol. 29, No. 5, pp. 1102-1113, 2013 [2] D. LAU, J. EDEN, Y. TAN, and D. OETOMO, “CASPR: A Comprehensive Cable-Robot Analysis and Simulation Platform for the Research of Cable-Driven Parallel Robots”, in Proc. IEEE/RSJ International Conference on Intelligent Robots and Systems, pp. 3004 – 3011, 2016 [3] D. LAU, “Initial Length and Pose Calibration for Cable-Driven Parallel Robots with Relative Length Feedback”, Cable-Driven Parallel Robots, Mechanisms and Machine Science, Vol. 53, pp. 140-151, 2017 [4] “XL-Laser: Large-Scale Cable-Driven Laser Cutting Robot” video
PROF. LAU TAT MING DARWIN
Department of Mechanical and Automation Engineering, CUHK
Dr. Darwin LAU is an Assistant Professor in the Department of Mechanical and Automation Engineering (MAE) at CUHK. In 2014, he received the Ph.D. degree from the University of Melbourne, Australia. He then worked in the Institute of Intelligent Systems and Robots (ISIR) at the University of Pierre Marie Curie, France, as a postdoctoral fellow.
Dr. LAU is a member of IEEE, member of ASME, junior chair of the IEEE Technical Committee on Mechanisms and Design in IEEE Robotics and Automation Society (RAS). He served as an Associate Editor for the IEEE International Conference on Robotics and Automation in 2017 and 2018, and also currently an Associate Editor for the Frontiers Journal in Mechanical Engineering and also IEEE Robotics and Automation Letters.